What is Asphalt Scarifier
Asphalt scarifiers, also known as the floor planers or floor milling machines, remove asphalt concrete surface very fast and aggressive. Their removal materials cover nearly all kinds of industrial stuffs: floor coating, glue, slurry, thermoplastic, paints, epoxy, rubbery elastomeric and etc. They are widely used in asphalt and concrete construction sites for floor preparation: erase traffic lines, eliminate floor height, generate adhesion, create grooves and so on.
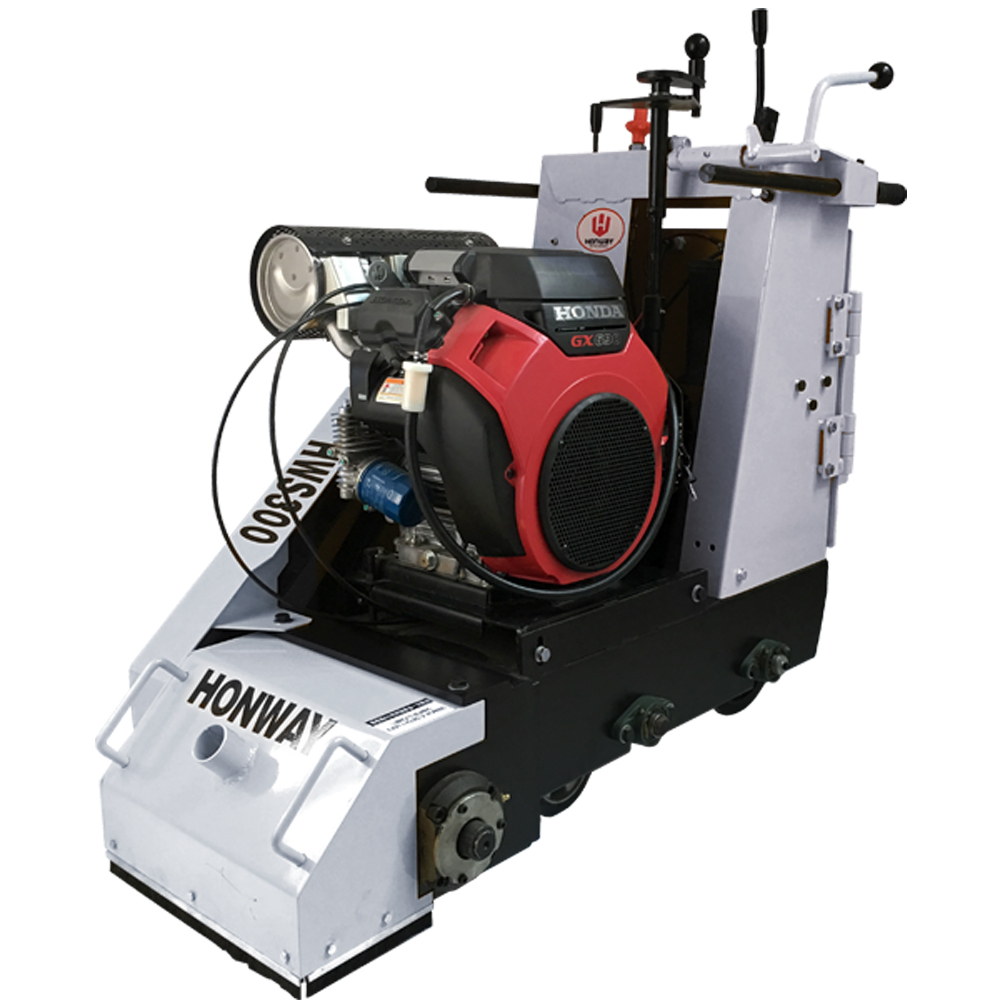
How does Asphalt Scarifier works?
The asphalt scarifier chip away the floor materials or make grooves very quickly because they make use of the pummeling action of the drum on the machine’s bottom. The drum consists of multi-tipped cutters, wheels, flails, at high speed to remove the asphalt and concrete surface. These cutters or blades are interchangeable. Their different combination achieves the profile which you need.
Six top brand of Asphalt Scarifier 2024
Graco
Graco manufactures and markets premium equipment to move, measure, control, dispense and spray a wide variety of fluid and powder materials.
Graco’s line of GrindLazer equipment provides a complete set of solutions for surface preparation applications so you get the job done right – in less time and with less effort.
Graco’s asphalt scarifiers are the choice of contractors looking to remove pavement markings, perform inlay grooving, and smooth uneven surfaces. Their pavement marking removal equipment delivers unmatched results while being able to handle the daily demands of professional contractors.
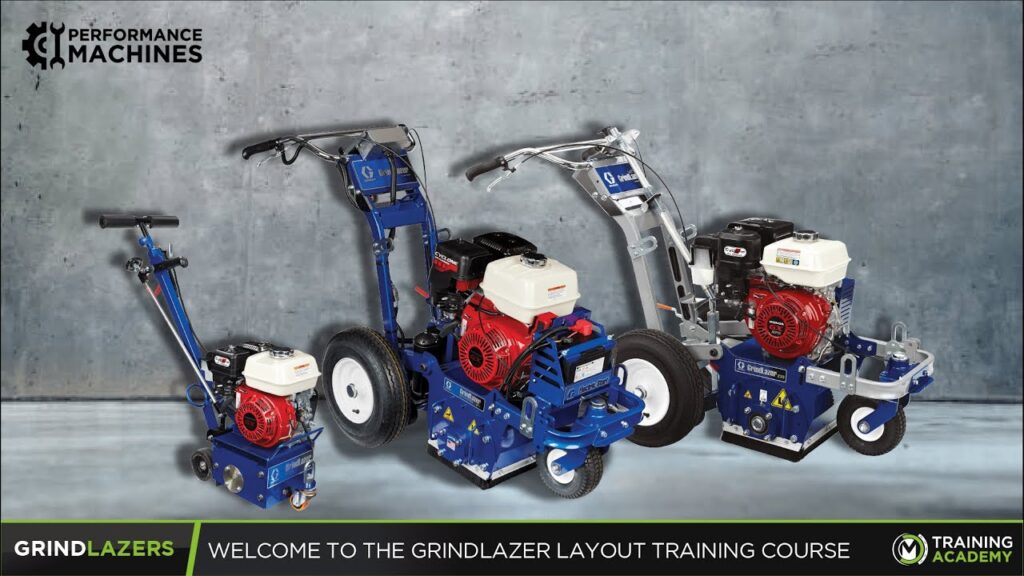
Honway
Honway has been in the field of asphalt and concrete scarification over 15 years. A large number of data on scarifying CSP (Concrete Surface Profile) has been accumulated. They are related with the combination and quality of cutters & blades, the technological design of machine, and knowledge of variable floor conditions.
With an in-house design & engineering team, the latest technology in raw material processing such as laser cutting, CNC routers, welding machines, thread drilling, saw blade cutting; and a well-organized OEM team the brand has the know-how and ability to provide OEM customers with solutions to their markets and applications. HONWAY team makes sure that all products designed to offer solutions to the end users, saving time and money due to smart & innovative features.
EDCO
Equipment Development Company (EDCO) is the manufacturer of American-Made surface preparation, removal, drilling, and sawing equipment. These machines include cutting tools for leveling, removing and scarifying surfaces. They solve common slab applications like unevenness, surface damage, surface marking removal, and sidewalk trip hazard repair.
EDCO line of scarifiers are designed to remove product from both concrete & asphalt as well as rapid removal of concrete or asphalt surfaces leaving behind a clean, textured but roughened finish.
SMITH
MITH Surface-Prep Solutions designs, builds, and delivers professional prep tools from their facility in Pompano Beach, Florida. SMITH equipment and tools help hard-working striping, pavement, and flooring contractors properly prepare surfaces to achieve all 10 surface profiles.
SMITH maintains the largest inventory of machines and consumable wear components for those with a variety of scarifiers, planers, grinders, line removers, routers, groovers, shavers, scabblers, and other prep tools.
For grinding sidewalk trip hazards, traffic-line removal, diamond shaving, planing and more, SMITH has the right tool for the job!
VEZOS
VEZOS was founded in 1970, designing and manufacturing pneumatic pumps for the marine and industrial market. Over the years VEZOS group expanded its manufacturing line offering innovative products to the contracting and road marking industries.
VEZOS Electric or gas walk-behind scarifiers with side loaded cutting drum, ideal for concrete surfaces, line marking removal, surface preparation & leveling and low gravity walk-behind scarifiers with perfectly balanced stability & design, ideal for industrial floor preparation with no skidding effect and Traffic scarifying models for road marking removal applications.
VONAX
The company of VONAX ARX Sweden AB is worldwide known in the area of floor surface preparation. During 80 years in business, they have collected tons of knowledge that they now base their operation and development around.
They are aware that a Scarifier is somewhat a commodity product and that there are many, many cheap products on the market. But Von Arx does not want to participate in that market.
What does the asphalt scarifierdo on asphalt?
Asphalt scarifier are widely used in floor and road constructions. The most common application on asphalt is to remove thermoplastic coatings, paint and traffic lines;
Unlike the traditional waterblasting that might damage asphalt, the asphalt scarifiers are designed to remove markings while keeping the surface intact. They can even be used on cracked surfaces. They achieve this by using a suspension drum on the machine bottom to float the multiple tipped cutters. It allows them to chip coatings off without damage the substrate or leaving the cracks.
Since they are walk behind model, 100-200kg, or self propelled model, 300-500kg, these high production asphalt scarifier are ideal for large volume applications at airports or municipalities as well as for stripping contractors who need rapid removal of marking from asphalt. They are designed with a 2’’ or 3’’ port to use with the vacuum cleaner for collecting dust and debris to keep jobsites clean and safe.
There is a note: Avoid removing the marking lines on asphalt in summer, as the high temperature might cause the asphalt soften, expand, even melt, which sticks to the cutters of the asphalt scarifier. It is very difficult to clean and reduces work efficiency. It is better to scarify after the temperature drop at night.
Asphalt scarifier has a few following characteristics:
1. The spindle bearing and design of bearing base can ensure that the machine adapts to the working condition of heavy load and high speed.
2. The drum is connected to the machine by the method of tension sleeve, which has large torque and shock resistance.
3. The quantity of drum’s rod and cutters. The more the cutters, the hihger working effectiveness.
4. The weight of the machine. The heavier the better, for protecting the machine from bouncing.